Global supply chain disruption
We contacted the University's purchasing department to find out more about the causes
Along with many others, we have been seeing supply chain issues emerging in recent years which are continuing to have an impact on deliveries to the University. We wanted to understand the wider context and the overall challenges faced by our suppliers, so we got in touch with colleagues in the University’s Purchasing Department (UPD) to find out more about the wider context of these issues and the challenges faced by the University and its suppliers.
What is the global supply chain?
The global supply chain is a vast interconnected network, developed and honed over the last few decades to support a ‘just in time’ world, where next day delivery is the norm. We have come to expect a huge amount of flexibility when purchasing goods, without any impact to timescales or price. While we all rely heavily on the global supply chain, we probably did not appreciate how complex it is, how far it reaches and how interconnected it is until more recently.
This article outlines some factors that have affected the global supply chain in recent years and will continue to have an effect through 2022 and beyond.
Geo-political impacts
The biggest impact on the supply chain for goods since 2020 has been the COVID-19 pandemic. The national lockdowns, beginning in East Asia and quickly spreading across the globe, hit the supply chain hard. Suppliers of raw materials, equipment manufacturers and major international transport hubs quickly shut down operations as the virus spread. This coincided with a massive leap in demand for certain goods. During the lockdown there was a huge requirement for scientific consumables and PPE equipment, but also an unprecedented shift to working or communicating remotely. This meant laptops, cameras, and other audio-visual devices were suddenly in high demand, resulting in buffer stocks being quickly depleted.
The pandemic also occurred soon after Brexit, which was already having an impact on the way goods and services were procured. The effects of Brexit on the supply chain were relatively minimal to begin with as. although there was additional red tape to navigate in respect of imports and exports, many items were still available from existing buffers of European and UK stock. A much bigger problem was the end of free movement of people.
Service industries in the UK had been relying heavily on European workers prior to Brexit and the end of free movement brought major gaps in capacity and skills. These labour shortages have resulted in either an inability to carry out services or a major deterioration in their quality.
Wider political situations have also had an influence. Very recently, the Russian invasion of Ukraine has started to have far reaching economic impacts. In terms of supply chain, the key areas affected are shipping and increasing prices.
Ukraine has one of the largest sources of titanium, magnesium and iron ore in the world and so a direct result of the invasion will be higher prices for these raw materials (impacting on the cost of items such as steel, aluminium, batteries, paints and inks, paper, and general products for the chemical, medical and construction industries). Russia is also the largest exporter of wheat, with constraints in supply impacting prices of staple foods. Energy and fuel prices are also being affected, with rises in the prices of these commodities impacting the cost of almost all goods and services. Russia supplies a third of Europe’s gas and the prospect of losing that amount of energy resource will likely force prices higher than those previously seen in winter 2021. Oil is currently valued over $100 a barrel, which directly affects consumer pricing. However, this could increase to $150 a barrel as hostilities continue.
We are yet to understand the full impacts of the economic sanctions on Russia and any actions that may be levelled in response, these could further impact the fragile global economy and impact the supply chain in terms of increased costs and prices for end customers.
Global inflation is also rising rapidly due to markets emerging from lockdown in addition to the events in Europe, therefore an increase in interest rates is likely. Some have predicted inflation rising to levels not seen since the early 1980s. This will ripple through the supply chain in terms of increased costs and prices.
Environmental factors
It is a widely accepted fact that extreme weather events are increasing and these events have a direct consequence on the supply chain.
Droughts in Taiwan are particularly significant to the IT market. Taiwan is one of the biggest manufacturers of semi-conductors for the global market and water is essential to the production of chips. It is used in vast quantities to purify the silicon and recent droughts have caused a 20 per cent reduction in output. Freak snowstorms in 2021 also affected silicon output in Texas. It should be noted, in this digital age silicon touches most products, from laptops through to electric cars and smart fridges, so the impact has been widely felt.
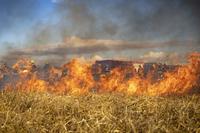
In Australia, wildfires have affected the extraction of raw materials including coal, oil, iron ore, gold copper and zinc, which feed the supply chain.
These are just a few examples of how environmental factors impact the production of raw materials and components. Without these materials and components manufacturers are unable to increase output to meet demand, and they have to compete with one another for a share of available materials.
Meanwhile hurricanes and tropical storms have affected movement of goods, especially sea freight – the most common form of transport from the Far East. In 2021, the effects of one container ship grounded in the Suez Canal had far-reaching consequences, but the impacts of hurricanes and tropical storms can be just as disruptive.
Shipping and logistics
Sea freight is the most widely-used form of freight to take goods from China to the rest of the world. Ports such as Shanghai and Shenzhen are incredibly complex sites, with continual movement of containers and vessels. When lockdowns were announced in China, these ports came to a sudden halt. This period of inactivity caused shipping containers to be stock piled, with limited means of processing them for onward shipment. As the world emerges from the pandemic, the ports are trying to unpick a complex logistical situation. Inevitably, costs are rising as a result. The price of shipping a single container was roughly £2k – £3k pre-pandemic. In 2021 that increased to £13k, with 2022 prices being approximately £11k.
To combat this situation manufacturers have been attempting to use the quicker option of airfreight. However, the obvious outcome is multiple companies competing for the same limited space. This has resulted in deals being made on the tarmac of the runway, with reports of shipments being ‘bumped’ from aircraft at the last minute to make way for more lucrative offers. Since the invasion of Ukraine, air freighters are avoiding Ukrainian, Belarusian and Russian airspace. It is likely that alternative flight routes will be directed towards the Middle East, which could quickly result in congestion and further delays.
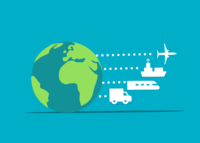
Rail freight is available to manufacturers, with the newly created Trans-Asian rail route, linking China to Europe and the Middle East. It is quicker than sea freight and cheaper than air. However, it too has been congested and is now threatened by events in Ukraine. Suppliers are quickly looking for alternative supply routes across the Pacific and Atlantic, but these are yet to be established as viable.
Shipping is also impacted by the geo-political factors mentioned earlier – chiefly Brexit-related issues such as domestic HGV driver shortages and rising fuel costs.
The outlook for 2022
The global supply chain is far from recovering the stock and supply levels of 2019. When manufacturing output has recovered and shipping routes are fluid, it is estimated a further six months will be required to refill global buffer stocks. Therefore, we can expect these issues to continue through 2022 and possibly beyond.
However, the uncertainty created by ongoing events in Ukraine will clearly delay, or potentially reverse, any recovery. Therefore, we can expect issues to continue through 2022 and beyond. Manufacturers are attempting to combat the situation by opening manufacturing sites outside the Far East to decrease dependency and shorten lead times, but this is a medium to long term solution (with many facilities not operational until 2023) and does not tackle immediate rising costs.
Suppliers will generally seek to pass on rising supply chain costs to protect their margin. While it is important that suppliers remain viable, and make a profit, it does not mean price rises should be accepted without question. Many suppliers will have been genuinely affected by the issues set out in this note, and can clearly explain the factors causing their price increases. Others take the opportunity to levy a price rise because the market will accept it. Therefore it is important to always ask for detailed justification for any price increase.
More news
Share this